|
|
|
|
|
https://www.ib-electronics.de
|
|
|
|
|
|
|
Die Fotodoku: Aufbau der neuen “Vicomte 1915:”
Meine erste Vicomte hatte über über 37 Flüge ohne Bruch absolviert. Die Tragflächen verzogen sich wegen der Holzleim-Seidenstoff Bespannung, je nach Temperatur und Luftfeuchte. Fliegen mit den luftfeuchteabhängig jedesmal anders verzogenen Tragflächen war ziemlich anstrengend. Die Maschine hatte dadurch eine teilweise unberechenbare “Tagesform”. Ich wollte das antik aussehende Flugmodell jedoch nicht in einem unbedachten Moment zu Bruch fliegen, deshalb entschied ich, einen Bausatz zu kaufen und ein gleiches Modell aufzubauen. Ich hatte berechtigte Hoffnung auf wesentlich bessere Flugeigenschaften. Der Bausatz besteht im wesentlichen aus diversen Balsaholzteilen und einem Bauplan. Leider war der Bauplan nicht so genau in seinen Abmessungen, also musste ich wirklich alle Teile und Abmessungen vorher auf Schlüssigkeit und Passgenauigkeit prüfen. Sogar die Zeichnung für die Tragflächen war in sich gekrümmt, wahrscheinlich war der Plan in der Produktion schon x-mal kopiert worden. Auch waren die Tragflächenhälften nach Plan über 10 mm unterschiedlich lang.
Die Holzteile waren unterschiedlicher Qualität und teilweise auch verzogen. Daher kaufte ich etliche Balsahölzer neu dazu, um ein wirklich gutes Bauergebnis zu bekommen.
Die Rippen für die Tragflächen waren sogar in falscher Anzahl vorhanden, einige waren zuviel, dafür fehlten die Endrippen. Etliche Teile gab es also aus Balsabrettchen nachzuschneiden. Bewährt hat sich das Zuschneiden der Holzteile mit einem OP-Skalpell, das ergibt schöne saubere Schnittkanten und hat sich besonders beim Zuschneiden der Verstrebungen des Rumpfes bewährt. Mit dem Skalpell lässt sich sehr genau arbeiten. ***** Aber Vorsicht - Skalpelle schneiden auch wunderbar leicht in Fingerkuppen ***** und noch etwas: abgenutzte Skalpellklingen zuerst in Klebeband einwickeln und dann erst in den Hausmüll geben.
|
|
|
|
|
|
|
|
|
|
|
|
|
|
Januar 2004, es geht los: der Rumpf wird gebaut.......
|
|
|
|
 |
|
|
Bild 2: der Bau beginnt, ich klebe die oberen 6x6mm Balsaleisten auf die Rumpfseitenteile.Für die gesamte Kleberei des Modells entscheide ich mich für Ponal Holzleim wasserfest.
|
|
|
 |
|
|
Bild 4: Einpressen und Kleben der unteren Balsaleiste. Fixiert habe ich sie mit Nagelschellen (Elektrikerzeug, geht prima) die ich dafür zweckentfremdet habe.
|
|
|
|
 |
|
|
|
Bild 6: Einkleben des Spant C (rechts oben) und Kontrolle der Rumpfhälften auf Symmetrie
|
|
|
 |
|
|
Bild 8: Einpassen des aus zwei Sperrholz- Platten zusammengeklebten Motorspantes
|
|
|
|
 |
|
|
Bild 11: Zusammenfügen der Rumpfenden. Da diese im flachen Winkel zueinander zulaufen, müssen die Leisten an der Berührungsfläche aufeinander eingeschliffen werden. Die Positionierung ist besonders sensibel, da bei Fehlern sofort ein Verzug im Rumpf auftritt und der Rumpf in sich verdreht sein kann. Deshalb ist der Rumpf auf seine Referenzfläche gelagert und mit Gewichten beschwert, bevor die Enden geleimt und gespannt werden..
|
|
|
|
 |
|
|
Bild 13: Die Streben werden an den Stirnflächen auf Passung eingeschliffen, damit der Verbinderpunkt kraftschlüssig geklebt werden kann.
|
|
|
|
 |
|
|
Bild 15: Die zusätzlichen X-Streben, sind nicht nach Plan, die habe ich zusätzlich angefertigt. Besonders knifflig dabei die Überkreuzung passgenau auszufeilen.
|
|
|
|
 |
|
|
Bild 17: es folgt das Aufkleben des Rumpfbodens, das ist etwas schwierig weil die Rumpfunterseite gewölbt ist. Zuerst werden die Leimraupen aufgetragen, dann die Beplankung aufgelegt
|
|
|
|
 |
|
|
Bild 19: erster Meilenstein, der Rumpf-Rohbau ist komplett geleimt und verschliffen, damit keine Kanten später durch die Folie drücken.
|
|
|
|
 |
|
|
Bild 21: die Führungsrohre der Bowdenzüge sowie das Antennenkabel für den RC-Empfänger habe ich durch mehrere kleine Holzleisten geführt, diese sind so im Rumpf geklebt das sich eine perfekte Fixierung der Rohre ohne Durchbiegeschwachstellen ergibt
|
|
|
|
Jetzt kommen die Tragflächen dran:
|
|
|
|
 |
|
|
|
|
|
|
|
|
|
|
|
 |
|
Bild 3: die unteren Leisten mussten zuerst in Wasser gelegt werden, bevor sie gebogen und auf die Kontur der Rumpfseitenwand geklebt werden konnten..
|
|
|
 |
|
Bild 5: jetzt werden die Fahrwerksaufnahmen und der Spant “B” eingesetzt und verleimt.
|
|
|
 |
|
|
Bild 7: probeweises Zusammensetzen der Rumpfseiten und Kontrolle auf Masshaltigkeit und Verzug, ich habe Glück, alles passt prima zusammen, keine Nacharbeit ist nötig
|
|
|
|
 |
|
|
Bild 10: Einpressen und Kleben des Motorspantes in den Rumpf. Da rüttelt später der Motor daran, deshalb muss diese Verklebung sehr gewissenhaft gemacht werden.
|
|
|
|
 |
|
Bild 12: Die ersten Verstrebungen werden sehr sorgfältig eingepasst, da durch den konisch zulaufenden Rumpf keine rechten Winkel zu finden sind. Vom Referenzbrett aus kann aber jede senkrechte Strebe auf 90° Winkel eingemessen werden, so das alle Streben zueinander einwandfrei winkelgerecht stehen.
|
|
|
 |
|
|
Bild 14: so entstehen die Streben des Rumpfteiles.
|
|
|
|
 |
|
Bild 16: Die Verstärkungen am Rumpf werden eingeklebt. Die Verstärkungen sind an der Verbindungsstelle zum Gitterteil des Rumpfes angebracht
|
|
|
 |
|
Bild 18: viele Bücher.......so wird die Beplankung möglichst gleichmässig mit Gewicht beschwert, bis der Leim ausgehärtet ist.
|
|
|
 |
|
|
Bild 20: der fertige Rumpf
|
|
|
|
 |
|
|
|
|
Bild 22 und Bild 23: die Grundstruktur der Tragflächen entsteht, nachdem ich die Leisten und Rippen auf der Helling gesetzt und geleimt habe.......
|
|
|
|
|
|
|
 |
|
|
Bild 24: die Tragflächen werden zusammen “verheiratet, wichtig ist dabei das die Flächen zueinander plan sind und die entstehende Tragfläche nicht in sich verdreht oder verzogen ist.
|
|
|
 |
|
|
Bild 26: hier seht ihr den Tragflächenstrack meines Riesenfluggerätes ;-) a touch of AIRBUS A380.....nein im Ernst, nur eine nette Fotoperspektive - Tragflächenrand noch ohne Randleiste
|
|
|
|
 |
|
|
Bild 28: Pinzettenjob, halten bis der Leim aushärtet.
|
|
|
|
 |
|
|
|
|
|
|
|
|
 |
|
|
Bild 25: klassische Laubsägearbeit! Randleisten aussägen und formen
|
|
|
|
 |
|
|
|
Bild 27: der Anschluss für die Randleiste wird vorbereitet, ich klebe sie einfach plan auf die zu einer Ebene geschliffenen Leistenüberstände.
|
|
|
|
 |
|
|
Bild 29: Schleifjob: mit Holzraspel, Feile und Schleifpapier die Randleisten fertig geformt und verschliffen. Geduld und Ausdauer bringt ein gutes Ergebnis.
|
|
|
 |
|
|
|
|
|
Bild 30 und Bild 31: Klebejob, Aufkleben der Mittelteilbeplankung und des Stirnblocks aus massivem Balsaholz.
|
|
|
|
|
|
 |
|
Bild 32: Schleifsklave: schon warmgeschafft im Abschleifen, geht es gleich weiter, nach dem Einkleben des Stirnblocks mit dem Formen des Frontblocks.
|
|
|
|
 |
|
Bild 34: jetzt wird die Tragflächenauflage eingepasst und eingeschliffen. Die Tragfläche soll ohne Druck durch die später eingesetzten Befestigungsschrauben schon ganz plan und wackelfrei auf dem Rumpf aufliegen.
|
|
|
 |
|
Bild 36: Was jetzt so nett aussieht war sehr schwierig, da die Beplankung sich vorne zur Nasenleiste hin krümmen muss und eine kunstvolle Spannerei mit Hölzchen, Brettchen, Büchern und Zangen nötig machte.. .
|
|
|
|
 |
|
|
|
|
|
|
 |
|
Bild 33: Frontblock der Tragfläche und Rumpf bei der Probepassung.
|
|
|
|
 |
|
|
Bild 35: linke und rechte Unterbeplankung der Tragfläche eingepasst und geklebt.
|
|
|
|
 |
|
Bild 37: nachdem der Tragflächenrohbau fertig ist, geht es gleich mit dem Rohbau des Seitenleitwerks weiter. Das ist simpel, alles flache Teile, alle Teile wie bisher mit dem Skalpell geschnitten und eingeschliffen.
|
|
|
 |
|
|
Bild 38 und Bild 39: Anfang April, der Rohbau des Seitenleitwerk und des Seitenruder sind nun fertig, erste gute Erfahrungen mit der Bespannung mit Bügelseide werden gesammelt.
|
|
Bilder 42 und 43 oben, sowie 44 und 45 unten:
Die Bespannseide sieht prima aus und lässt sich sehr gut verarbeiten. Als Bügeleisen dient ein kleines Reisebügeleisen von Rowenta. Ein spezielles Bügeleisen ist für solche Bügelarbeiten nicht notwendig. Mit der Temperatureinstellung - Baumwolle- ergeben sich einwandfreie Bügelergebnisse wenn man wie folgt die Bügelseide verarbeitet:
Die Folie mit 3cm Übermass zuschneiden, nicht zu sparsam sein, denn man bekommt die Kanten nur dann gut hin wenn der Überstand mit den Fingern noch gut fassbar und daher während des Anbügelns gut ziehbar ist. Zuerst die Folie auflegen und mit Stecknadeln fixieren. Keine Sorgen, die Stecknadeln verursachen keine sichtbaren Löcher in der Folie, auch nicht beim Darüberbügeln. Zuerst sollten das Folienstück umlaufend an den Kanten angebügelt werden. So kann die Folie nicht mehr verrutschen und was noch wichtiger ist, durch die Randfixierung kann man eine wirklich makellose Fläche erbügeln. Durch die Randfixierung erreicht man ein vorgegebenes, sehr gleichmässiges Zusammenziehen der Folie im nächsten Arbeitsschritt .
Jetzt mit dem Heissluftfön die ganze Fläche gleichmässig und langsam erwärmen. Auf die Folie achten, das sie sich gleichmässig beginnt, zusammenzuziehen. Durch weiteres Erwärmen auf Spannung bringen und als Finish noch einmal mit dem Bügeleisen über die Fläche gehen, damit die Rippen auch sich mit dem Kleber der Folie verbinden. Die überstehenden Folienränder dann mit einem scharfen Skalpell abschneiden. Die französische Tricolore des Seitenleitwerks ist eine selbstklebende Dekorfolie die zum Schluss appliziert wird. .
|
|
|
|
|
|
|
|
|
|
 |
|
|
Bild 44:
|
|
|
|
 |
|
|
Bild 46: ca. 3 cm Übermass sind gut, dann kann man beim Anbügeln schön an der Folie ziehen.
|
|
|
|
 |
|
|
Bild 48: Das Brandschott wird mit selbstklebender Aluminiumfolie bekleidet, die Bohrungen für Motorträger und Schlauchdurchführungen gesetzt.
|
|
|
|
 |
|
|
Bild 50: der graue Schaumstoff ist mit dem Skalpell auf die Form des Tanks ausgeschnitten und umschliesst den Tank beim Einsetzen nur so fest, das die späteren Motorvibrationen nicht zur Schaumbildung des Kraftstoffs im Tank führen werden.
|
|
|
|
 |
|
|
Bild 52: der Empfänger ist nun in seiner Schaumstoffwanne eingebettet und auch die Servos für Gas, Höhe und Seite haben ihren Platz gefunden, i
|
|
|
 |
|
|
|
Bild 54: Einbau des GFK Motorträgers
|
|
|
|
 |
|
|
Bild 56: Antriebseinheit Gesamtansicht, die graue Gemisch-Regulierschraube im Vordergrund unterhalb des silbernen Kraftstoffilters.
|
|
|
|
Der Propeller ist ein 9x5” Nylon auf einen Aluspinner , Motor mit Nylonträger, Prop und Spinner wiegen 325 gramm.
Die Besonderheit des hängenden Einbaus verursacht kaum Probleme beim Betrieb, wenn das Tankniveau dem niedriger liegenden Vergaser angeglichen werden kann.
Im Tank sollte unbedingt ein Sinterfilterpendel (Krick oder Simprop) statt dem normalen Messingpendel verwendet werden, da kleinste Blasen im Kraftstoff den OS schnell zum Stehen bringen würden und das Standgas sonst zu hoch eingestellt werden müsste. Die Tankleitung wurde später wegen dem Einbau des Kavan Tankventils geändert, kommt jetzt unterhalb der Gemischnadel aus dem Brandschott
|
|
|
|
 |
|
|
|
 |
|
|
|
|
|
|
|
|
|
|
|
|
|
 |
|
|
Bild 45: die Folie mit grosszügigem Übermass zuschneiden und auflegen, an der Stirnseite etwas anbügeln, anschliessend am Rumpfende spannen und dort ebenfalls anbügeln.
|
|
|
|
 |
|
Bild 47: jetzt umlaufend den Folienrand etwas spannen und die Folie entlang des Randes anbügeln. Zum Schluss die Fläche mit dem Heissluftfön erwärmen und noch einmal mit dem Bügeleisen von vorn bis hinten die Folie an den Rumpf bügeln
|
|
|
 |
|
Bild 49: Führungsrohr des Gaszuges sowie die Bodenauskleidung für den Tank werden eingebaut
|
|
|
 |
|
Bild 51: aus einem Schaumstoffblock wird mit dem Skalpell eine Schaumstoffwanne für den Multiplex Micro IPD Empfänger zugeschnitten. Die Schaumstoffwanne ist perfekt zur schwingungsarmen und festen Lagerung des Empfängers,der sich dennoch leicht herausnehmen lässt.n
|
|
|
|
 |
|
Bild 53: Ich bin ein Fan von Kugelgelenkanschlüssen, das ist etwas aufwendiger, sieht aber nicht nur gut aus, sondern funktioniert auch sehr langlebig. Daher habe ich mir für den Anschluss der Bowdenzüge an die Ruderhörner der Servoantriebe eine Kombination aus Kugelgelenk (Krick) und Löthülse (Graupner) einfallen lassen. Das Gewinde der Löthülse passt perfekt in den Kunststoffteil des Kugelgelenks. Das Gestänge wird dann mit Sekundenkleber in der Schraubhülse verklebt, es ist damit absolut sicher gegen Herausrutschen
|
|
|
|
 |
|
Bild 55: Der OS LA25 wird hängend eingebaut. Links daneben der silberne Kraftstofffilter.
|
|
|
 |
|
|
Bild 57: Druckschlauch zwischen Tank und Schalldämpfer sowie Dosselklappenanlenkung
|
|
|
|
Einlaufprogramm für den OS LA25:
natürlich muss jeder neue Motor zuerst “einlaufen”, ein sehr wichtiger Prozess bei dem sich alle Motorteile aufeinander “einreiben” Je nachdem wie sorgfältig diese Einlaufphase gestaltet wird, bekommt der Motor seine Qualität hinsichtlich, Anspringverhalten, Leistung und vor allem Lebensdauer.
Nach erstmaligem Start wurde in relativ fetter Einstellung nach jeweils 30 Minuten Laufzeit allmächlich auf ein etwas höheres Leistungsniveau gesteigert. Die ersten 30 Minuten fanden bei 1/3 Gasstellung statt, dann 30 Minuten bei 50%, dann 30 Minuten bei 75%. Die Einlaufzeit betrug gesamt 1,5 Stunden (echte Betriebszeit ohne Unterbrechungen). Versorgung aus separatem Tank. Danach 2 Minuten Höchstleistung. Verwendeter Propeller 9x5.
|
|
|
|
Bild 58 rechts:
In der Bildmitte: der automatische Kavan Zweiwege Tankanschluss. Der Anschluss ist sehr praktisch zum Be- und Enttanken und vermeidet die Sauereien durch verschütteltes und herumtropfendes Nitromethan.
weiter Rechts: die gelbe Schraube ist eine angebrachte Verlängerung der Gemischnadel, die Schraube steht 2mm durch die Cowling etwas hervor und so kann die Nadel von aussen jetzt leicht eingestellt werden. Schraube cw (clockweise ) im Uhrzeigersinn = Gemisch verarmen, Schraube ccw ( counterclockwise ) gegen den Uhrzeigersinn = Gemisch anreichern = fetter
unterhalb der Gemischschraube: Die Cowling ist mit insgesamt 4 Schrauben an Sperrholzaufnahmen angeschraubt. Zur Vibrationsentkopplung habe ich in die passend gebohrten Löcher der Haube die Gummitüllen eingesetzt, die auch für Servobefestigungen verwendet werden. So habe ich schon die Cowling der Vorgängermaschine befestigt und niemals Risse in der Haube gehabt.
|
|
|
|
 |
|
|
Bild 59 und Bild 60: die geänderte Kraftstoffzuleitung nach Einbau des Kavan Tankventils oben links jetzt zusehen. Die Cowling wurde mit einem Streifen ABS verlängert, dazu habe ich mehrere Stege aus Epoxy-Leiterplattenmaterial mit jeweils 4 Stück Schrauben und Muttern M2 angebracht. Diese Konstruktion ist sehr stabil und vibrationsfest und hat sich in beider alten Vicomte schon bewährt. Das Spaltmass zwischen Cowling und Prop beträgt nur 3mm!!
|
|
|
|
|
 |
|
|
Bild 61: jetzt geht es langsam auf den Erstflug zu!!
|
|
|
|
30.07.2004 - Jetzt kommt der Tag..........
|
|
|
|
|
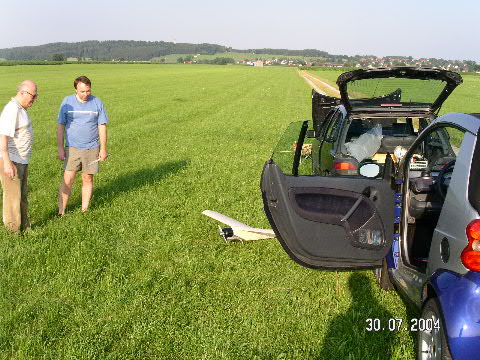 |
|
|
|
Bild 62:
Es ist der 30.07.2004 Mein Fliegerspezl Jean-Pierre und ein älterer Herr der gerne mal vorbeikommt, wenn wir auf unserer Fliegerwiese sind.
Der Erstflug beginnt, ich war so aufgeregt, das ich leider kein Video davon gemacht habe. Nach dem Betanken und Überprüfen der RC Anlage, der Motorleistung sowie der Ruderaussschläge setzen wir die Vicomte auf den geteerten Weg neben der Wiese und lasse sie nur mal kurz hüpfen um die Reaktion beim Start zu sehen. Alles geht gut, sie bricht kaum aus.
Dann überprüfen wir nochmal die Maschine und setzen sie auf die Piste. Das Herz klopft jetzt schon sehr, etwas zittrige kalte Händen halten die Steuerknüppel des Mutliplex Cockpit MM RC Senders.
|
|
|
|
|
|
 |
|
Bild 63: jetzt geht es langsam auf den Erstflug zu!!
|
|
|
|
|
|
Hebel nach Vorn, Vollgas, etwas Seitenruder rechts, die Vicomte beschleunigt, ich ziehe etwas Höhe, sie reagiert spät und steigt dann schön mit 25° in den Himmel. WOW!
Anschliessend in ca 50m testen wir die Maschine, die Trimmung, die Fluglagen, Verhalten auf die Steuereingaben und finden das alles ziemlich gut passt.
Das Startverhalten des OS war am Anfang etwas zickig, mit zunehmender Betriebsdauer springt er besser an, allerdings startet der OS nur gerne mit Motorstarter. Engegen der Meinung “alter Hasen”, finde ich die Startmethode von Hand sowieso nur eine Qual für Prop, Motor und Aufhängung. Das von mir bei anderen Modellfliegern beobachtetet Geklopfe und Herumgeschlage auf den Propeller tut mir manchmal schon sehr weh. So etwas ist von vorgestern.
Ein Motorstarter startet Modellmotoren wegen der gleichmässigen Drehzahl viel schonender und man kann zudem das Startverhalten besser beurteilen, als die Finger-Quirl-Rühr-Methode.
|
|
|
|
|
|
 |
|
|
Bild 64: ....nach 6 Monaten Bauzeit.....hier fliegt sie!
nach einigen Flügen bei denen ich die Servowege noch geringfügig verändert habe, hat sie jetzt ein wunderbares Flugbild. Durch die Exponentialkorrektur antwortet die Vicomte auf Steuereingaben originalgetreuer und gleicht nicht mehr dem hektischen Geflatter manch´ andere Taxi-Trainer. Das Modell soll im Flugbild eher einem historischen Oldtimerflugzeug entsprechen.
Folgende Einstellungen und Daten habe ich vorerst erflogen:
Höhenruder: +/- 15 mm, zusätzlich 35% Exponential Seitenruder: +/- 35 mm, zusätzlich 30% Exponential
Technische Daten:
Vicomte 1915, Balsaholz Gitter- und Stäbchenkonstruktion mit Bügelseide bespannt, Motor in hängender Position, zweiachsgesteuertes Modell,
Propeller:.........................APC Type 9x5 Motor:..............................OS LA25 Spannweite:.....................1600mm Flächeninhalt gesamt: ......470dm² Gesamtgewicht:................1482 gramm (unbetankt) Flächenbelastung:...........31,55gramm/dm²
|
|
|